24
2025
-
07
喷涂线能耗占比分析:这3个环节最值得优化
作者:
创智涂装
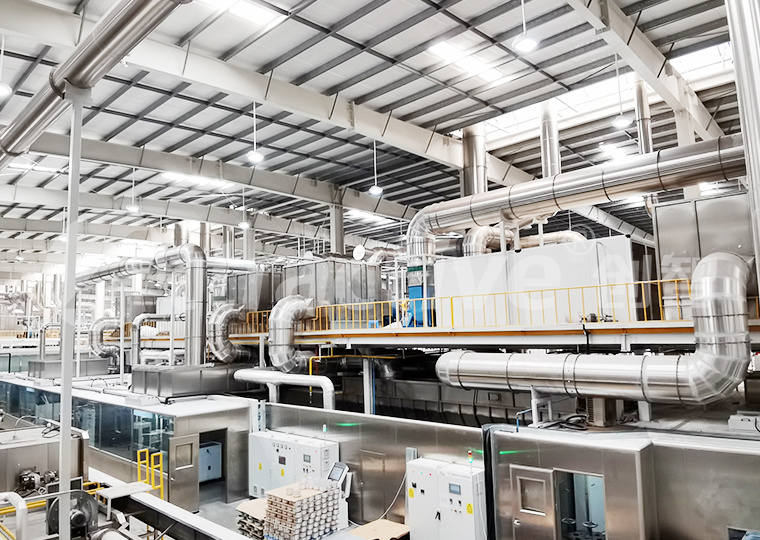
一、涂装生产线能耗现状分析
现代涂装生产线通常由前处理、喷涂、烘烤等多个工艺段组成,每个环节都会产生不同程度的能源消耗。根据行业调研数据显示,在典型的涂装生产线中,烘烤固化环节能耗占比高达40-45%,喷漆室运行约占30-35%,前处理系统则占15-20%。这三个环节合计能耗超过总能耗的85%,是节能改造的重点方向。
值得注意的是,不同企业的具体能耗分布可能存在差异,这主要取决于生产工艺、设备选型、生产节拍等因素。因此,在进行节能改造前,建议先对生产线进行全面的能耗审计,准确掌握各环节的能耗情况。
二、烘烤固化环节:余热回收技术是关键
1. 传统烘烤工艺的能耗问题
烘烤固化作为涂装线烘烤优化的核心环节,其能耗问题主要体现在以下几个方面:首先,传统烘烤工艺的废气温度常达200℃以上,造成巨大能源浪费;其次,烘烤炉体保温性能不足导致热量散失;再者,工艺参数设置不合理也会增加能耗。
2. 先进节能技术应用
目前最有效的RTO余热回收方案,通过特殊设计的蓄热体将烘干废气中的热量回收利用,可预热新风至150℃左右,热效率可达95%以上。某知名汽车制造商采用这项技术后,烘烤段天然气消耗量降低了38%。
低温固化涂料是另一项重要突破。以80℃固化的阴极电泳漆为例,相比传统160℃固化工艺,不仅能耗降低45%,还能减少VOC排放。某汽车配件厂采用"底漆免强冷+湿碰湿"工艺后,成功取消2道烘烤工序,年节省电费超80万元。
3. 烘烤工艺优化建议
定期检测烘烤炉密封性能
优化烘烤温度曲线
采用分区温控技术
加强操作人员培训
三、喷漆室运行:循环风技术突破能耗瓶颈
1. 喷漆室能耗构成分析
喷漆室节能的重点在于空气循环系统。在典型喷漆室中,空调能耗约占60%,排风系统占25%,照明等其他设备占15%。传统设计的新风换气量往往超出实际需求,导致空调负荷居高不下。
2. 循环风技术应用案例
通过部署循环风技术(机器人喷涂区80%空气循环利用),某家电企业成功将新风处理量从50000m³/h降至36000m³/h,空调能耗降低28%。配合干式喷房的石灰粉漆雾收集装置,该企业喷房宽度缩减15%,供风系统电耗同比下降22%。
3. 其他节能措施
采用变频控制的风机系统
优化喷漆室气流组织
使用高效过滤材料
实施智能化控制系统
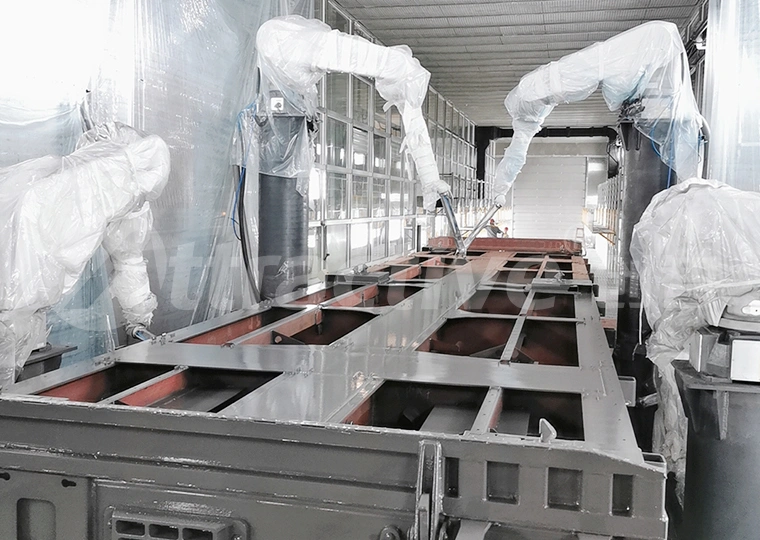
四、前处理系统:无磷工艺降低综合成本
1. 传统前处理工艺的局限性
在涂装线前处理优化领域,传统磷化工艺存在能耗高、污染大等缺点。处理槽液通常需要加热至35-40℃,且会产生含磷废水,增加后续处理成本。
2. 新型环保技术应用
突破性的无磷转化膜技术(如氧化锆预处理)正在快速普及。某金属制品企业改用氧化锆工艺后,前处理段蒸汽消耗减少60%,废水处理费用降低45%。对于精密部件清洗,CO₂雪花清洗技术可替代部分水洗流程,使前处理阶段运营成本降低50%。
3. 工艺优化方向
推广常温前处理工艺
采用逆流漂洗技术
实施槽液在线监控
优化生产节拍
五、综合节能方案实施路径
1. 短期措施(1-3个月)
进行能源审计和热成像检测
优化设备运行参数
加装变频控制系统
开展员工节能培训
2. 中期改造(3-6个月)
引入余热回收系统
升级喷漆室循环风技术
改造照明系统
实施能源管理系统
3. 长期规划(6-12个月)
采用新型低温固化涂料
建设智能监控平台
考虑可再生能源利用
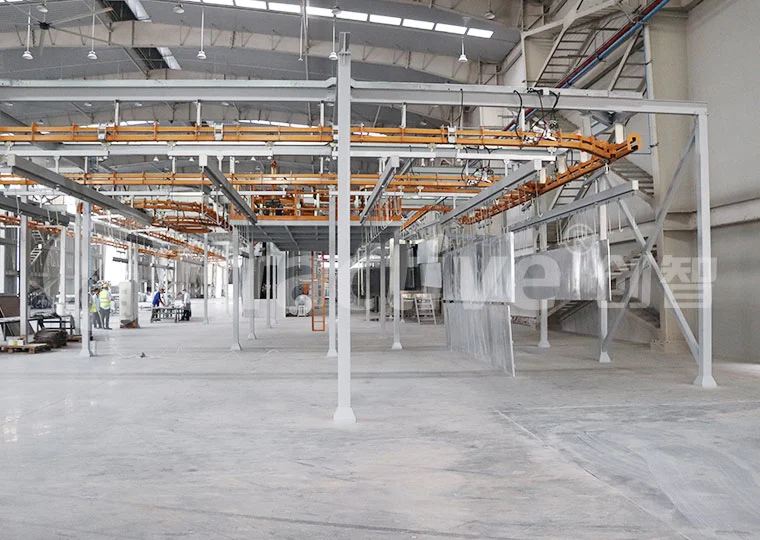
六、成功案例分享
某大型家电制造企业通过对涂装线进行全面节能定制升级,取得了显著成效:
1. 烘烤段:安装RTO余热回收系统,年节约天然气费用120万元
2. 喷漆室:采用循环风技术,空调电耗降低25%
3. 前处理:改用无磷工艺,废水处理成本下降40%
整体改造投资回收期仅2.3年,年综合节能效益达280万元。
七、未来发展趋势
随着技术进步,涂装生产线节能将呈现以下趋势:
1. 智能化能源管理系统普及
2. 新型环保材料广泛应用
3. 工艺整合简化流程
4. 可再生能源利用率提升
涂装生产线的能耗优化是一个系统工程,需要从工艺、设备、管理等多个维度着手。通过聚焦烘烤固化、喷漆室运行和前处理系统这三大关键环节,企业可以显著降低生产成本,提升环保绩效。我们建议企业根据自身情况,制定分阶段的节能改造计划,必要时可寻求专业机构的支持。
喷涂线能耗占比分析:这3个环节最值得优化
相关资讯